Social Responsibility
Commercial Furniture Solutions recognises, a small footprint can have a lasting effect for future generations.
Our business doesn’t exist in isolation nor is it simply a way of making money. Our employees depend on our business.
Customers, suppliers and the local community are all affected by us and what we do. Our products, and the way we make them, have an impact on the environment. It means taking a responsible attitude, going beyond the minimum legal requirements and following straightforward principles that apply whatever the size of your business.
Customers, suppliers and the local community are all affected by us and what we do. Our products, and the way we make them, have an impact on the environment. It means taking a responsible attitude, going beyond the minimum legal requirements and following straightforward principles that apply whatever the size of your business.
Our Commitment
CFS is committed to reducing its impact on the environment and all the company’s products are developed with this, key criteria in mind. Many years from now, when our products have lived long and satisfying lives, it will be time to recycle them. All parts used in the manufacture of these products can be disassembled and used in the recycling process.
We are committed to pursuing the highest standard of environmental performance, consistent with our position as a leader in design and manufacture of commercial seating. Our goal is to minimise our manufacturing ‘footprint’.
CFS is continuously adopting waste and emission minimisation, resource conservation, recycling and sustainable development through the manufacturing process and selection or raw materials. All statutory and company regulations are strictly observed.
All employees are educated and made aware of the environmental implications of their actions. We are continually monitoring and updating appropriate technology in relation to environmental management.
This document inclusively describes all of the warranties given and remedies available with respect to the company’s products and services. CFS disclaims any other warranty whether express or implied, statutory or otherwise, in relation to the products. The warranty period starts from the date of purchase.
CFS tests Customer’s Own Material (COM) and other customer-supplied items such as upholstery materials for manufacturing quality only and does not provide any warranty with regard to these materials. The warranty on fabrics and foam is limited to that given by the manufacturer, agent or supplier.
CFS is committed to reducing its impact on the environment and all the company’s products are developed with this, key criteria in mind. Many years from now, when our products have lived long and satisfying lives, it will be time to recycle them. All parts used in the manufacture of these products can be disassembled and used in the recycling process.
We are committed to pursuing the highest standard of environmental performance, consistent with our position as a leader in design and manufacture of commercial seating. Our goal is to minimise our manufacturing ‘footprint’.
CFS is continuously adopting waste and emission minimisation, resource conservation, recycling and sustainable development through the manufacturing process and selection or raw materials. All statutory and company regulations are strictly observed.
All employees are educated and made aware of the environmental implications of their actions. We are continually monitoring and updating appropriate technology in relation to environmental management.
This document inclusively describes all of the warranties given and remedies available with respect to the company’s products and services. CFS disclaims any other warranty whether express or implied, statutory or otherwise, in relation to the products. The warranty period starts from the date of purchase.
CFS tests Customer’s Own Material (COM) and other customer-supplied items such as upholstery materials for manufacturing quality only and does not provide any warranty with regard to these materials. The warranty on fabrics and foam is limited to that given by the manufacturer, agent or supplier.
CFS’s products meet the requirements of Federal and State Laws. To the extent allowed by law, any implied warranties, including any warranty of merchantability or fitness for a particular purpose, are disclaimed and to the extent they are legally required, are limited in duration to the duration of this written warranty.
CFS shall not be liable for loss of time, inconvenience, commercial loss, or incidental or consequential damages. CFS will not be liable for any loss or damage (including costs) however caused, whether direct or consequential, incurred or suffered by the purchaser or any third party in respect of the products but nothing contained herein will or will be considered to exclude or restrict any liability on CFS’s part for death or personal injury resulting from negligence.
CFS shall not be liable for loss of time, inconvenience, commercial loss, or incidental or consequential damages. CFS will not be liable for any loss or damage (including costs) however caused, whether direct or consequential, incurred or suffered by the purchaser or any third party in respect of the products but nothing contained herein will or will be considered to exclude or restrict any liability on CFS’s part for death or personal injury resulting from negligence.
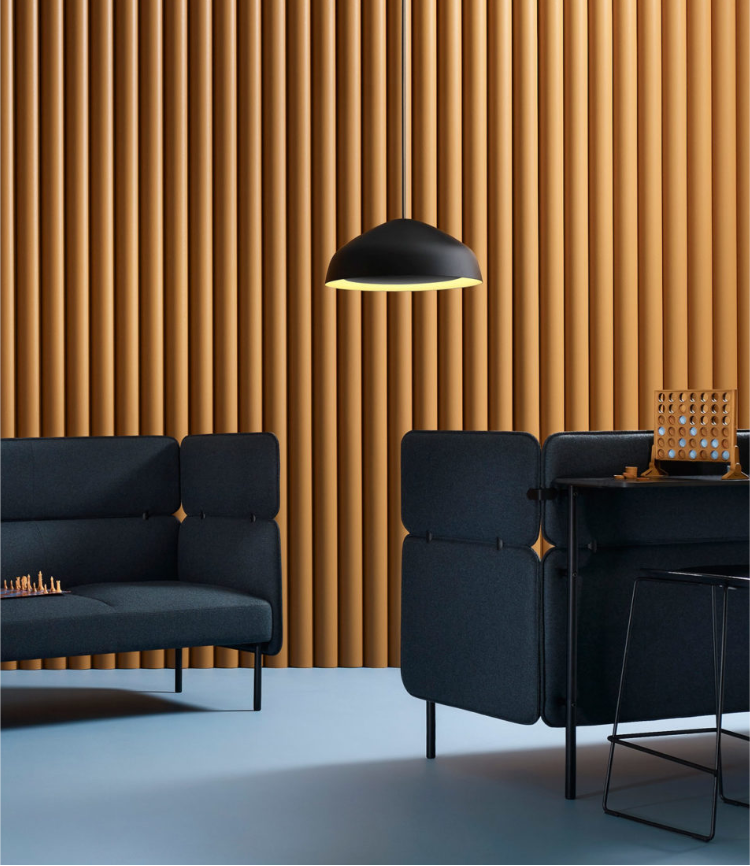
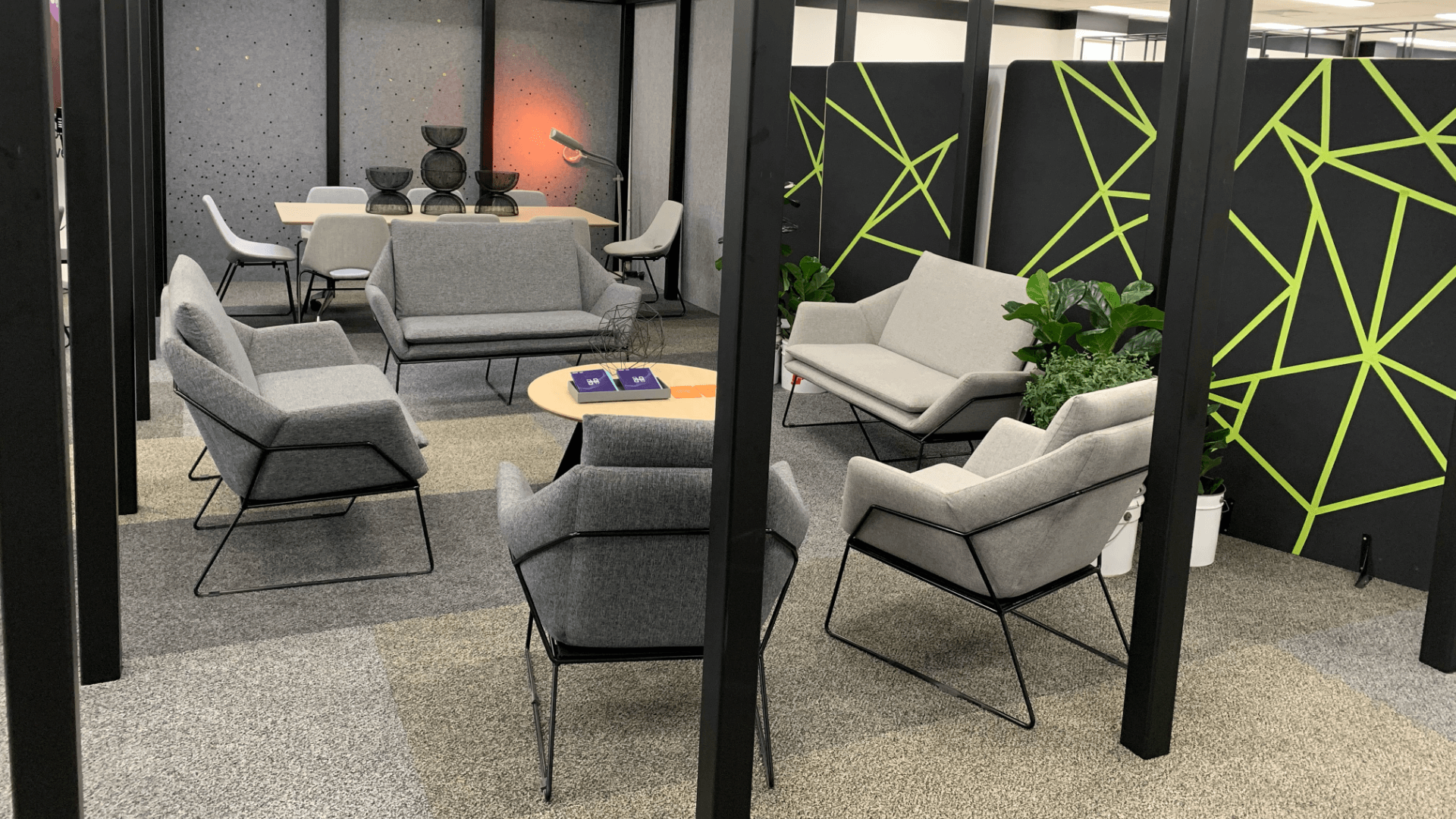
Timber Material
CFS works with its major supplier of timber products to ensure that Australian made MDF comes from government and privately owned plantations. Hardwoods used are also certified through the Australian Forestry Standard (AFS). The AFS was developed to provide a system for the certification of sustainably produced forests and wood products.
Powder Coasting
CFS powder coating of the steel frames is carried out by approved and certified operators ensuring that the highest environmental standards are maintained. Our powder coaters are regularly and independently tested for compliance to EPA regulations. The powder used in the powder coating process is TGIC free
CFS works with its major supplier of timber products to ensure that Australian made MDF comes from government and privately owned plantations. Hardwoods used are also certified through the Australian Forestry Standard (AFS). The AFS was developed to provide a system for the certification of sustainably produced forests and wood products.
Powder Coasting
CFS powder coating of the steel frames is carried out by approved and certified operators ensuring that the highest environmental standards are maintained. Our powder coaters are regularly and independently tested for compliance to EPA regulations. The powder used in the powder coating process is TGIC free
Safety commission
CFS uses Australian made MDF to ensure that it complies with the low formaldehyde emission level E1 defined in the Australian Standard AS/NZS 1859.2:2004 for MDF. The wood content used in the MDF is 60% preconsumer recycled and 40% reclaimed silviculture fibre. This means that the emissions are well below the workplace exposure limit set by the National Occupational Health and Safety Commission.
Recyclable
At the end of our product lifespan, our customers can be confident that all steel parts, timber parts and plastic parts used in the manufacturing process can be separated and sent for recycling.
Due to the fact that some items require professional disassemble, arrangements can be made with CFS to carry this out, thus simplifying the recycling process and reducing the environmental impact.
CFS uses Australian made MDF to ensure that it complies with the low formaldehyde emission level E1 defined in the Australian Standard AS/NZS 1859.2:2004 for MDF. The wood content used in the MDF is 60% preconsumer recycled and 40% reclaimed silviculture fibre. This means that the emissions are well below the workplace exposure limit set by the National Occupational Health and Safety Commission.
Recyclable
At the end of our product lifespan, our customers can be confident that all steel parts, timber parts and plastic parts used in the manufacturing process can be separated and sent for recycling.
Due to the fact that some items require professional disassemble, arrangements can be made with CFS to carry this out, thus simplifying the recycling process and reducing the environmental impact.